Airborne & Structure Borne Ultrasound Survey & Inspection Services
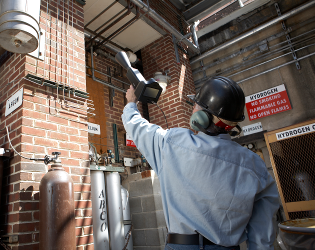
Ultrasound Leak Detection Services
Pressure or vacuum systems, seals and gaskets, wind noise, hatch leaks, vacuum bagging, compressed air, compressors, valves, steam traps, heat exchangers, boilers, condensers, building envelope, glove box, distillation columns
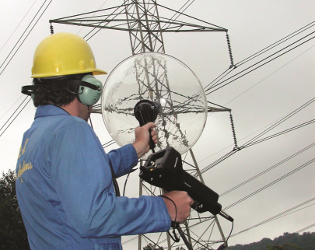
Ultrasound Electrical Inspection & Testing Services
(All voltages, open access or enclosed) Arcing, tracking, corona, partial discharge: switchgear, transformers, arresters, insulators, motor control centers, distribution lines, buss bars, breakers/disconnects
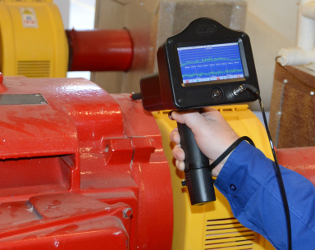
Ultrasound Mechanical Inspection Services
Bearing faults (all speeds), lack of lubrication, prevent over lubrication, compressors, pumps (cavitation), motors, gears/gear boxes, hydraulic systems, fans, couplings, trending, trend reports, spectral analysis
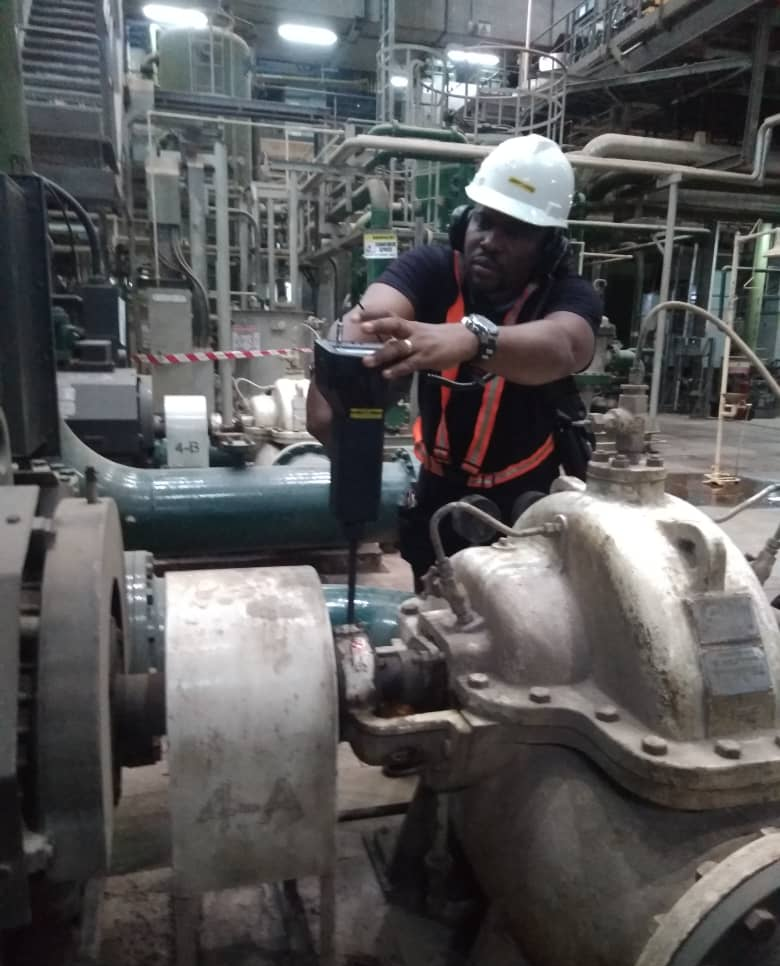

AIRBORNE & STRUCTURE BORNE ULTRASOUND SURVEY & INSPECTION SERVICES
Airborne ultrasonic scanning is rapidly becoming accepted as an effective nondestructive testing method. It is a predictive maintenance/energy conservation technology used to locate leaks, detect electrical emissions and to inspect mechanical conditions in operating equipment. Instruments based on this technology senses high frequency sounds produced by targeted equipment, leaks and electrical discharge that are above human perception (20 kHz-100 kHz) and electronically translates these signals by heterodyning them down into the audible range where they can be heard through headphones and seen as intensity increments on a meter or display panel.
Although the ability to gauge intensity and view sonic patterns is important, it is equally important to be able to “hear” the ultrasounds produced by various equipment. That is precisely what makes this itechnology so popular. All operating equipment, most leakage and electrical problems produce a broad range of sound. The high frequency ultrasonic components of these sounds are extremely short wave in nature. A short wave signal tends to be fairly directional. It is therefore easy to isolate these signals from background plant noises and to detect their exact location.
The basic advantages of ultrasound and ultrasonic instruments are:
- They are directional and can be easily located
- They provide early warning of impending mechanical failure
- The instruments can be used in a loud, noisy environment
Ultrasonic scanning performed by our experienced ultrasonic technicians provide another valuable tool to your preventative and predictive maintenance programs and will help reduce the potential for both personal injury and equipment downtime.
Typical applications include:
- Compressed air leak detection, vacuum leak detection and steam trap inspection,
- Mechanical condition inspection, bearing testing
- Detection of arcing, tracking and corona in electrical equipment.
ASSETMATRIX employs both direct contact ultrasonic testing and airborne ultrasonic testing in the following areas:
- Airborne non-contact ultrasonic testing of high voltage equipment to detect arcing, tracking and corona discharge.
- Direct contact ultrasonic testing of bearings to measure noise output in decibels to determine bearing performance and to develop a history for future reference.
- Leak detection in valves, vacuum systems, steam traps, vessels, heat exchangers, gaskets and seals as well as ductwork.
ASSETMATRIX combines ultrasound and infrared thermography to provide the ultimate maintenance inspection service. A combined program of Infrared Surveys and airborne ultrasonic scanning provides significant insurance against an unscheduled outage, equipment damage or a fire. Our inspection service will save money and provide confidence in the safety and functional ability of the inspected equipment.
ASSETMATRIX Predictive Maintenance and Condition Monitoring services using Ultrasound technology includes:
LEAK DETECTION:
Pressure or vacuum systems, seals and gaskets, wind noise, hatch leaks, vacuum bagging, compressed air, compressors, valves, steam traps, heat exchangers, boilers, condensers, building envelope, glove box, distillation columns,
MECHANICAL INSPECTION:
Bearing faults (all speeds), lack of lubrication, prevent over lubrication, compressors, pumps (cavitation), motors, gears/gear boxes, hydraulic systems, fans, couplings, trending, trend reports, spectral analysis
ELETRICAL INSPECTION:
(All voltages, open access or enclosed) Arcing, tracking, corona, partial discharge: switchgear, transformers, arresters, insulators, motor control centers, distribution lines, buss bars, breakers/disconnects